As part of Particle Technology’s ongoing improvement changes, our internal cleanliness testing department has now implemented test method TM102 Issue 3 to further align our oil cleanliness/ non-volatile hydrocarbon (NVH) / non-volatile hydrocarbon residue (NVR) testing specifications by incorporating a rotary evaporator into our processes.
What is a Rotary Evaporator?
A Rotary Evaporator is a laboratory device used to remove solvents from samples through the evaporation process.
Working on the principle of reducing the pressure on a sample, which can cause the solvents to evaporate at a lower temperature than their typical boiling point. A sample is placed into a round bottom flask that is then rotated at a constant speed.
Using a heated water bath or mantle the solvent then evaporates leaving behind the sample.
The evaporated solvent is then condensed and collected in a separate flask. The temperature and pressure of the system can be controlled to optimise the evaporation process.
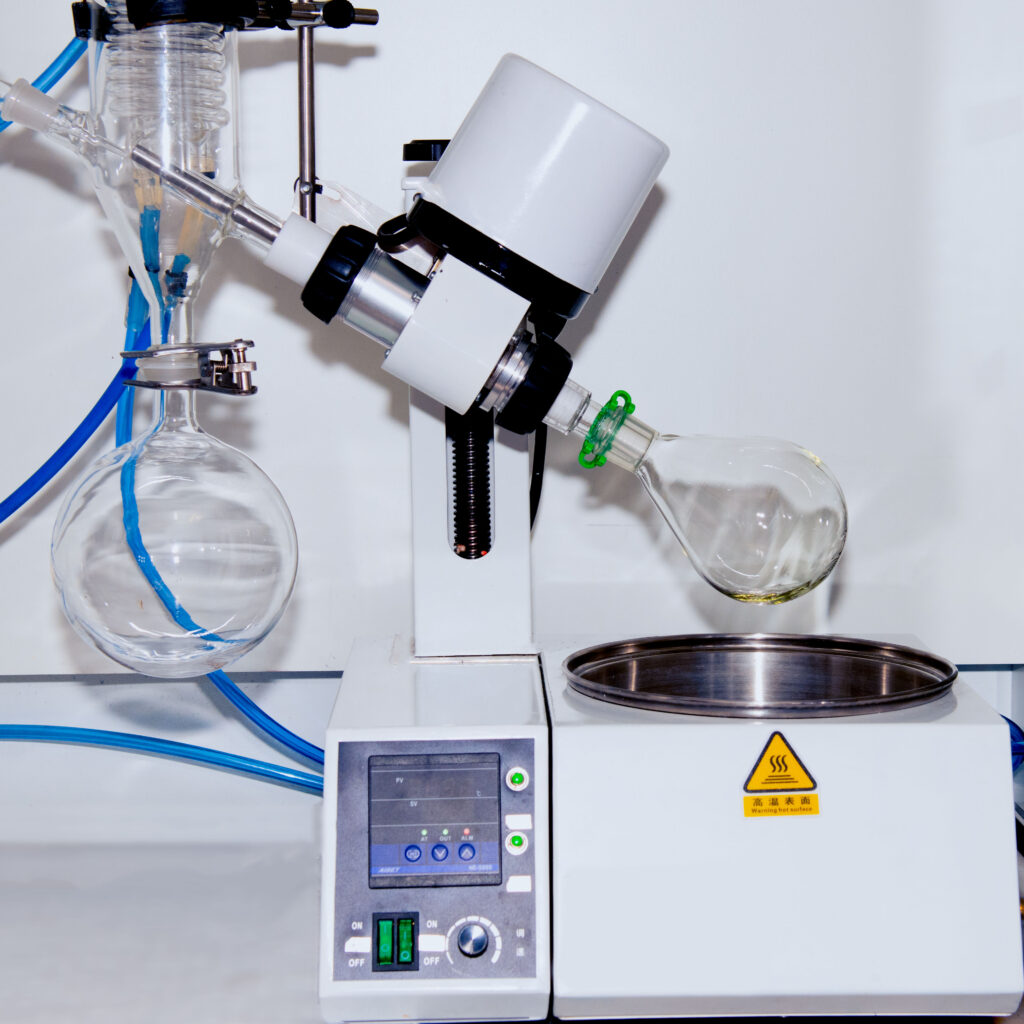
Use in Cleanliness Testing
One key area for improvement for our cleanliness testing process is by better controlling flammability and harmful vapour hazards.
Using a distillation method provides a safer option and due to the ability to recycle excess vapours, also offers a more environmentally friendly approach.
The use of a rotary evaporator in cleanliness testing is based on the fact that residue and contaminants can be dissolved into solvents and then the solvents can be evaporated using the rotary system.
Rotary evaporator testing is suitable to test the cleanliness of products such as medical devices, food packaging and automotive components.
Implementation and Conclusion
As part of implementing this change to our cleanliness procedures, a valid blank result and distilled solvent was measured.
The purpose of this validation procedure is to determine the suitability of this equipment to the testing related standards.
The conclusion of the validation procedure showed that the cleanliness of the blank result is satisfactory to the oil cleanliness/ non‐volatile hydrocarbon (NVH) / non‐volatile hydrocarbon residue (NVR) related standards.
Further to this due to the 25‐50% retained distillate there has been a reduction of waste solvent and provides a more efficient process.
As part of a recommended action further test conditions will be trialled to improve both the cleanliness and distillation efficiency.
Results
Vessel 1 – A target value of <1mg oil contamination was achieved on the primary evaporation vessel.
Vessel 2 – The distilled vessel showed a total target weight of 0.1mg oil contamination and a recycled distillate quantity of between 25 and 50%.
Through our innovative new procedures in accordance with the latest TM102 standard, we are able to improve the cleanliness levels of parts, helping to enhance product quality, lifespan, and overall customer satisfaction.
If you would like any more information about Cleanliness Testing or other services and products from Particle Technology, please browse our website or get in touch today.